My childhood was spent on Sunfish Creek in southern Ohio. It was where I learned how to swim, where I cast my first fishing line, and where I caught my first crawdad. My grandfather, Clyde, owned some of the property along the creek, so it was a private oasis for our family. The creek is one of the major tributaries into the Ohio River. I would not learn what this really meant until much later in life.
Aluminum is one of the most common metals used worldwide today. Recently, there has been a big push to use more aluminum-based products for sustainability. In fact, big corporations like Coca-Cola, PepsiCo, and Apple have announced their plans to start using recycled aluminum to show their commitment to sustainability. This is good for the environment because aluminum can be recycled indefinitely. So, why do I see hospitals and contaminated rivers when I see aluminum products?
I grew up in a small southern Ohio town not far from the Ohio River. Our backdrop was the West Virginian hills leading to the Appalachian Mountains, which lit up in the fall with vibrant reds, oranges, and yellows. Summers were spent splashing in creeks and catching lightning bugs. In the evenings, we would watch the sunset on the river as the barges and towboats floated down. Along the river was also the Ormet Corporation, which made aluminum and resided in Hannibal, Ohio. It was essentially the sole employer in the Monroe County river towns. All the men in my family worked there, and although the work was hard, it was considered a great place to be employed. At the time, Ormet was the fourth-largest aluminum-producing company in the United States, so they had great benefits and paid well.
While we do not give it much thought, aluminum is actually the most abundant metal on Earth, making up more than 8% of the matter in the Earth’s crust. However, it is rarely found in its pure form. It is mostly found in rocks, minerals, and clays. Aluminum and its various salts and oxides have been used since the Roman Empire. The material we know today, however, was not formally discovered until 1808 by Humphry Davy, when he unsuccessfully attempted to isolate it through a process called electrolysis. Following his lead, Hans Christian Ørsted isolated aluminum successfully by reduction of aluminum chloride in 1825. Twenty-nine years later, Henri Sainte-Claire Deville would advance the aluminum reduction process even further to produce higher quantities of metal. Finally, in 1886, Charles Martin Hall and Paul Louis Toussaint Héroult simultaneously developed the smelting process for aluminum, which we still use today.
This is the same process Ormet used when it opened in 1957 in Hannibal, Ohio. Spurred by government incentives, Ormet became the first company to join Alcoa, Kaiser, and Reynolds as the largest producers of aluminum in the United States. During this time, government incentives were created due to the aluminum shortage, which resulted from all the aluminum used for the Korean War. However, the government overestimated the amount of aluminum the country required, which led to a surplus. The military developed less of a need for aircrafts that relied heavily on aluminum. Instead, they needed more materials for missiles, which required more durable, heat-resistant metals. The aluminum industry found new ways to help alleviate the surplus through the introduction of aluminum cans, aluminum foil, and mobile homes. Nevertheless, the aluminum industry was seriously depressed through the 1960s. Regardless of this depression, though, Ormet was producing about 360 million pounds of aluminum per year at the time. Due to the high levels of production, the plant needed upgrading to be more cost-effective. As a result, in December 1964, the owners created the Olin Revere Realty Company, the purpose of which was to provide land, buildings, and equipment for Ormet.
My grandfather, Clyde, was hired the same year Olin Revere Realty Company was created. He was tall, lean, and tan, and unbeknownst to him, was also about to meet his second wife, Molly, my bonus grandmother. I still have not met anyone who worked as hard as he did. When he wasn’t at Ormet, he worked at his sawmill, on cars or tractors, or was helping his sons build their homes. He was gentle but stern in a way that only works for grandfathers. He would spend hours in the evenings sitting at the kitchen table teaching my brother and me how to play rummy and euchre. I remember helping my grandmother pack his lunches in that same kitchen. However, long before that he was working on the pot lines.
The “pots,” as everyone called them, were electrolytic cells made of carbon-lined steel pots measuring twenty feet long, ten feet wide, and fourteen inches deep. These pots could resist heat and the corrosive effects of the fluorides. In the pots, the aluminum oxide was reduced to an almost pure metallic aluminum in a bath of molten fluorides at a temperature of approximately 1800°F. Anodes made of carbon are used to conduct electricity into the pots. These anodes are consumed in the smelting process, and the remaining portions are then recycled. These anodes are attached to copper rods, which eventually were also consumed. So, at intervals of about every fourteen days, the molten aluminum is tapped from the pots and transported to the cast house at a temperature of just over 1292°F to form ingots.
However, these high temperatures were not the only dangerous parts of the job. When Ormet began production in 1958, asbestos materials were also popular because they were the cheapest and most efficient way to prevent fires inside these plants that maintained such high temperatures. Asbestos was used for everything from insulation for pipes, wiring, and even safety gear to lining the pots. Ormet employees handled the material without any safety gear and rarely wore masks to avoid inhaling asbestos fibers. Raw asbestos fibers, known as “dough balls,” were used to stop molten aluminum from escaping the furnaces. In addition to the asbestos exposure, Ormet employees were exposed to contaminated drinking water. Ormet used five disposal ponds on site to dump their hazardous waste materials. From 1958 to 1968, Ormet dumped around 85,000 tons of spent potliner, a dangerous by-product of aluminum production which contains cyanide, was placed in unlined disposal ponds. Because these ponds were unlined, the waste leaked out and contaminated the employees drinking water as well.
When helping pack my grandfather’s lunches, my grandma would sometimes let me help make his sandwiches. Asbestos would fall on these sandwiches as the employees were eating their lunches. Clyde said sometimes they would blow it off their food, but most of the time, they were too tired to bother and just ate it. It wasn’t until 2004 that the Ohio EPA ordered Ormet to remediate all the asbestos. By then, however, it was too late for many employees. The rate of Mesothelioma among Ormet employees was very high. Mesothelioma is a rare and aggressive form of cancer that primarily affects the lining of tissue that covers the majority of your internal organs, most often affecting the tissue that surrounds the lungs. It is caused by exposure to asbestos fibers. Clyde lost many friends to this horrible cancer.
Molten aluminum is tapped from each pot every thirty-two hours at a rate of approximately one ton per pot. Tapping the pots requires a tapper and a setter. Tappers remove the molten aluminum from the bottom of the pots by placing a vacuum tap through an end access port, forcing the molten aluminum into a large evacuated crucible. Each pot takes thirty minutes to one hour to tap, and the tappers are also responsible for cleaning the crucible. The setter then removes spent carbon anodes and uses a sledgehammer to remove the excess carbon. They then place fresh anodes into the pots with the assistance of an overhead crane.
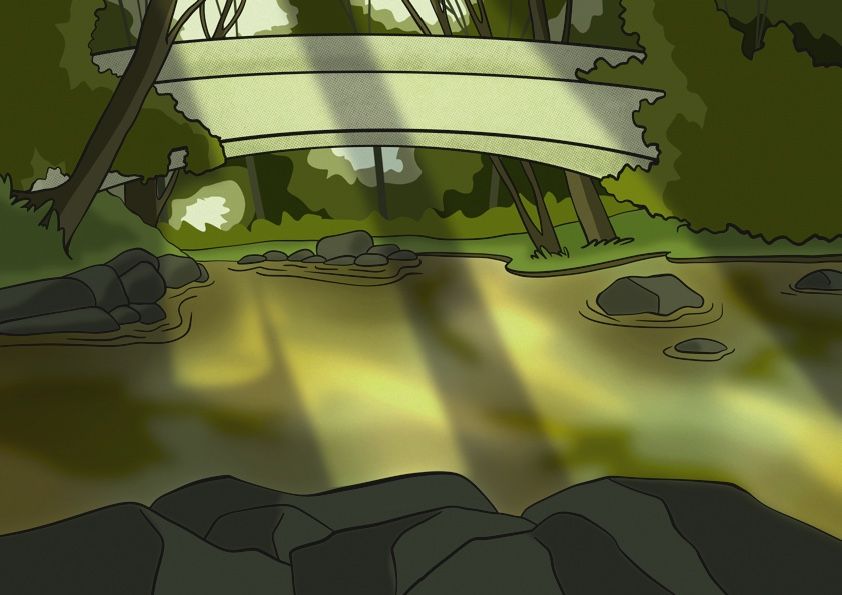
Ormet used Ranney Wells for their employees’ drinking water and their heating exchange systems to cool the aluminum. A Ranney Well is a water well system that includes a central chamber with horizontal perforated pipes extending out into an aquifer. According to the EPA, Ormet knew by 1966 that the water drawn from its Ranney Well was contaminated with twenty-four parts per million of fluorides, an amount that is as much as twelve times the drinking water standard of the time. By July 1971, the water in this Ranney Well turned black and contained high levels of fluorides. The contamination was attributed to the caustic liquid wastes (fluorides and cyanides) leaching from the unlined disposal ponds found on the same site and the spent potliner storage area. Former Ormet Chief Chemist Joseph Baretincic pointed out this was a massive problem for the plant because it used about 1,800 gallons of water per minute daily. At the same time, former Ormet Project Engineer Bernard Paidock characterized the situation as an emergency because the plant could not continue to operate using this contaminated water.
Around this same time, my grandfather married his second wife, Molly. My dad was about ten years old then and soon received two younger brothers in quick succession. They grew up knowing never to eat anything they caught out of the Ohio River because it was contaminated entirely by then. It wasn’t just Ormet contaminating the river; coal mines and chemical companies like DuPont were found all along the river as well. There have been efforts to clean up the river since the 1950s; however, it remains the most polluted river in the United States even today. It was also around this time that my grandfather was promoted to pot service cranemen. He operated the overhead cranes that were used to move spent rods from the pots, position new carbon anodes, transport and add alumina from portable bins, and move all the equipment for the tapping operation. It was a much better position because it was much less physical than working the pots, although he was still working in the extreme temperatures of the pot rooms.
Aluminum has never fallen out of fashion because it is almost infinitely recyclable. All materials lose some volume as part of the melting and recycling process. However, with aluminum, only a tiny amount of metal is typically lost through this process, ranging from 0.1% for products like can sheets to 3.9% for products like foil. In fact, a comprehensive industry analysis shows that nearly 75% of all the aluminum ever produced is still in use today. Recycling the material takes about 90% of the energy it takes to make new aluminum. Of course, aluminum cannot alleviate all of our environmental concerns. The Aluminum Association says Americans still send more than $700 million worth of aluminum cans to landfills yearly.
The Ohio EPA classified Ormet a “major discharger” in May 1980 under the federal Clean Water Act, so it was required to have its outfall discharges tested by an independent laboratory. That report, provided to the Ohio EPA in June 1981, revealed that Ormet was discharging high concentrations of complex cyanides into the river. After the Ohio EPA became aware of the cyanides, Ormet developed a process to treat the contaminated water before dumping it into the Ohio River. Then, in an October 1982 letter to the Ohio EPA, Ormet reported that a water treatment plant would cost an estimated $2,500,000. So, they argued against implementing the treatment because of the costs. Because no action was taken after this, the United States Environmental Protection Agency nominated Ormet in September 1985 for inclusion in their National Priorities List (“NPL”). The NPL is a list of the nation’s worst pollution sites that warrant remedial actions. These remedial actions fall under the remediation processes outlined in the Comprehensive Environmental Response, Compensation, and Liability Act (“CERCLA”), otherwise known as the “Superfund.”
During this time, there was also a significant recession in the United States, which caused Ormet to file for Chapter 11 bankruptcy protection in 1982. However, Ormet emerged in 1985 when it hired a new president, E. Emmett Boyle. Boyle, along with his management team and a group of investors, formed the Ohio River Associates, Inc. to buy Ormet. The deal was almost complete when the plant was hit with a strike by 1,500 members of the United Steelworkers, which delayed the sale until September 1986. Clyde was one of the strikers. During this time, the plant was run by a skeleton crew of less than 300 people. The strike continued until early 1989, when the steelworkers were able to strike a deal for better wages and benefits. Ormet was then reopened, but because about half the smelting operation had been put out of commission, Boyle had to borrow almost $14 million to restart the company. However, aluminum prices quickly rebounded, and Boyle and his group invested in modernization and other improvements. By 1993, Ormet had invested more than $70 million in capital improvements, all of which were drawn from profits rather than borrowed.
A few years after these investments made Ormet profitable again, my dad, Tim, started working for Ormet in 1997. Clyde was so happy to get to work with his son. The family all gathered, and we had a huge BBQ. Like all new hires, Tim had to start as a setter. I remember him coming home wholly exhausted the first year. Eventually, he got used to the work, or my twelve-year-old brain stopped registering his physical distress. After some time working there, Tim was promoted to overhead craneman, then moved to a mechanic role. He would work on everything from weed eaters to thirty-ton cranes. Not unlike my grandfather, my dad was a tinkerer. He was intelligent and naturally curious, which made him good at most things. So, it is easy to see why this role suited him best, not only because of his experience as a mechanic but also because he got to do something different every day.
In the late 1990s, Ormet sought to increase its diversification by investing in capital improvements and external growth. In 1996, Ormet created the Ormet Railroad Corporation, a 13-mile stretch of railroad track from the Hannibal location to Powhatan, Ohio. The following year, Ormet bought a majority interest in Formcast, Inc., a Denver, Colorado-based semi-solid metal caster. Ormet also added to its recycling capabilities that same year by acquiring SPL Recycling LLC and Vortex Corporation. However, all this growth came to a quick stop with the economic downturn in the early 2000s. By 2004, Ormet once again had to file for Chapter 11 bankruptcy protection. The company submitted a reorganization plan to the bankruptcy court and at the same time, Boyle submitted his resignation as CEO. Michael Williams then took the CEO position and restructured the company. This change lasted only a short time, though, as Williams was quickly replaced in 2006 by Ken Campbell.
In 2010, Clyde was diagnosed with mesothelioma, and in 2011, he finally agreed to try chemotherapy. I remember sitting with him during one of these treatments, wondering if the aluminum that made up the IV pole came from Ormet. There is no way to accurately describe what it is like to watch a loved one waste away from cancer. My grandfather was my hero, so it was bittersweet when he passed in 2012. The funeral home was too small for all Ormet coworkers who came to pay their respects. People had to wait outside and take shifts coming in and out. It was a silver lining on a very hard day, seeing how many people thought as highly of my grandfather as I did. His obituary proudly claimed forty-two years of service at Ormet Corporation.
Around the same time, Ormet was once again hit with low aluminum prices and high power costs, and it proved to be a storm Ormet could not weather again. In a statement released to the press, Chief Executive Mike Tanchuk said, “Ormet has done everything possible during very difficult financial times to pay its debt and legacy obligations. However, with a low metal price and higher power costs, we no longer have the financial liquidity to continue to do this.” According to the court filing, Ormet listed total liabilities of $416 million and assets of $406.8 million. On July 31, the final and permanent closing of Ormet Primary Aluminum Corporation was announced.
This closing put over 3,000 people out of work and cut off another 1,000 Ormet retirees from their benefits. While the plant might not have been the best workplace or the most environmentally sound company, it did support much of the Ohio Valley. Without Ormet, Monroe County became a welfare county, which was exacerbated by a wave of methamphetamine and opioid addiction. However, over the last couple of years, it has become a hotbed for oil and gas companies which has brought the economy back up for everyone living in the rural area.
Recently, Long Ridge Energy Terminal broke ground on the 1,600-acre property for a 485-megawatt power plant to cover about 25 acres of the property. The Ohio River still holds the title of the most contaminated river in the country, but it also still holds a very special place in my heart. I am happy that the site is being remade into something new and is creating jobs for all the people that are still there. I also recognize the importance of aluminum for our environment. However, I do not think I will ever be able to see it as the environmental hero that everyone else sees.